2024
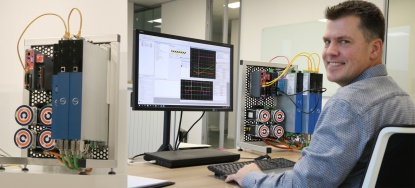
From challenge to opportunity with Stöber safety technology
A safe machine with minimal downtime, without compromises on performance because safety techniques throw a spanner in the works. “That sounds...
Date: 7 August 2020
The company Wadcon Automation, located in Groningen, specializes in the construction of special machines for the automation industry. From one of her customers she received the order to realize a new machine for cutting glass fiber reinforced plastic, called Pecolit. This material is by definition difficult to fabricate, so the process was performed manually with a sawing machine. Due to increasing production numbers, this became physically heavier and the fabric production higher, so they decided to purchase a machine for this process.
Chris van der Velde (project manager at Wadcon) started working on this with his team. After research, they came to the conclusion that the process should be carried out by cutting instead of sawing, also called “slitting”. This is a scissor movement, but with a rotation. With the correct adjustment the dust production is minimal. For the new machine Chris started looking for servo drives that must run synchronously with each other.
‘The implementation of this project has come true thanks to intensive and valued cooperation with ATB Automation. The offered solution brought significant – unexpected – benefits!’
The slitting machine
A slitting machine has been developed to cut the material Pecolit into strips. For the construction of this machine, various automatic process steps have been defined to automate the production process.
A roll with Pecolit is manually fed into the machine by an operator. The machine is laterally enclosed by roller bars, which can be moved at the backside. The material is trapped by moving the rear roller bars forward. The material is implemented by means of a liftable construction for the transition rolls, which are driven by a Stöber servo geared motor. This is the starting point for starting the machine.
When the process has started, the above-mentioned drive implements a plate until it sees a sensor. The encoder value from the Stöber servo geared motor starts to measure the distance traveled at this point. This is also the moment when the three sets of slit wheels come into action. Most eye-catching are the Stöber servo motor gearboxes that realize the slitting movement. By choosing Stöber bevel gear reducers with hollow shaft, the slit wheels can be attached directly to the gearbox shaft, making the construction much more compact.
All slit drives follow the speed of the implementing transport. The above Stöber servo motor gearboxes come into operation, after which the implementing transport pushes the plate through the wheels and 'slits' the Pecolit in long strips.
For the lighter drives in the slitting machine, the compact right-angle low-cost Wanshsin servo gear units were chosen. These are assembled with the Stöber EZ3 servo motors. This allows the use of the modular servo system from Stöber consisting of the EZ servo motors and multi-axis SI6 controllers. The 15 servo drives in total are controlled with a Trio Flex-6-Nano Motion Controller equipped with EtherCAT. This controller is the perfect and compact combination for precise synchronization.
Rolling up the slitted material is really special: by pushing the slitted material against suction cups on a “drum”, a starting situation is created in which the material is pulled tight against the drum on the one hand, while on the other hand this guarantees that the strips will not be wrapped over each other.
The challenge
The process for slitting Pecolit isn’t difficult, however the application contains a number of topics that could cause some problems. To begin with, many calculations need to be executed, such as positioning the slit wheels.
The machine contains two servo geared motors for implementing the material, which is then slit by six slitting wheels. One of the challenges was to ensure that the rotations of the shafts are synchronized so that the material does not bulge, get pulled too much or ‘run off’ to one side. To make this even more complex, each slit wheel can be ground, which changes the diameter. Furthermore, the material that has been slit is rolled up, here the speeds of the drive are extremely accurate.
The solution was to achieve synchronization of the slitting wheels by coupling all wheels to the shaft of the material implementing wheels. The diameter of each slitting wheel is known, this is used to calculate the transmission ratio of the axle settings. When inserting a new piece of material, the material is clamped between the input wheels. When a sensor is used, the position at which the material passes the sensor is very accurately remembered by registering the input.
A good combination
Wadcon has had a good relationship with ATB Automation since 2010. After presenting the principles fort he servo drives to ATB Automation, they worked together to select the best configuration. The choice is made for ATB Automation because of the complete package of products and because of the expertise in selecting the most optimal solutions. A big plus was that parts could be saved, which resulted in a favorable cost.
‘ATB Automation is a reliable supplier who stands for the products that are delivered. Both during the selection of the components and during their commissioning. The accessibility and support is excellent. The employees of ATB Automation are on the same wavelength as those of Wadcon. We think together in solutions in each other's field in order to be able to create the most optimal product. This project is an excellent example of this!’
Who is Wadcon?
Wadcon Automation designs and realizes special machines aimed at the manufacturing industry. They have their focus on three product groups: assembly machines, production machines and (duration) testmachines.
The company is founded in 1989 as an engineering firm and over the years she has specialized in the construction of special machines, where solution scan be found widely in the market.
We supply slewing ring bearings, oscillating mountings, tensioner devices from stock and we also have spiral bevel gearboxes, servo gears and electromechanical actuators in our delivery program.
In addition we also select and offer the right components and systems for motion control solutions, such as servo gear motors, linear servo actuators and complete XYZ cartesian systems.
ATB Automation uses cookies to give you the best browsing experience possible on our site.
Continue to use the site as normal if you agree to this.
We use cookies on our website to create the most effective website possible for our users. Cookies are small text files that are sent to and stored on your computer, smartphone or other device for accessing the internet, whenever you visit a website. Cookies allow for us to measure and personalise. The cookies we use allow us to improve your experience when using our website and ensure the website performs as you expect it to. It also allows us to offer eg videos on our website and display social media share buttons. On this site, the cookies we use include 'analytics' cookies, to analyse how users use this site to help us make our website better for those who visit it regularly.
The settings below allow you to specify which cookies you accept. Please note that by not accepting all cookies, some parts of the site will not work properly.