2024
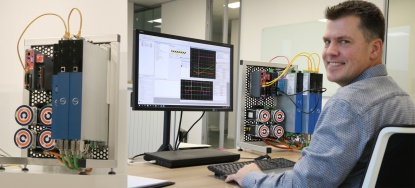
From challenge to opportunity with Stöber safety technology
A safe machine with minimal downtime, without compromises on performance because safety techniques throw a spanner in the works. “That sounds...
Multi axis servo drives with one centralised power supply. The SI6 drives are available in mono axe and double axis modules and can be connected in many numbers on one dc-bus voltage with the limit of 200A. The concept is very small: a double axis module of 2 x 5 Amps is only 45 mm width.
The very fast contoller has a position, speed and current cycletime of 62,5 µs.
Due to the compact design many space can be saved in the electrical cabinet.
The SI6 drive is available with the following dimensions(w x h x d)
The PS6A power supplies are availabe in two sizes:
Via the handy Quick DC-Link system the drives are on one DC bus connected to the power supply. Energy fed from one drive can therefore be used for the acceleration of another drive. As a result, energy is saved and the power supply can be dimensioned lower. The power supply can work with one central resistor that can also be dimensioned lower.
The Quick DC-Left system is placed behind the power supply and drives, and connected via a copper conductor rails of 12 x 5 mm up to a maximum of 200A. When one power supply is not sufficient, three pieces PSA624 or six pieces PSA634 can be used parallel.
The SI6 drives can also be linked with the SD6 controllers by using the Quick DC-Link. For example, when more powerfull drives are required (above 50A nominal). When also the power supply of the SD6 drive size 3 is adequate for the SI6 controllers there is no separate PSA6 power supply needed.
When one of the two-axis drives is not used for 100% of its nominal current, it is possible to use the other drive with a higher current as nominal. For example, when for one axis nominally 3A is required for the second axis nominally 6A may be applied to the two-axis SI6A062 (2 x 5A nom). This allows a heavier drive is saved.
The SI6 inverters are suitable for servo motors with following feedback:
For use with EnDAT 2.2 and EnDAT 3 are the Stöber EZ servo motors with electronic nameplate available.
A resolution of more than 33 million positions per revolution (37 bits) can be achieved.
The SI6 is equipped with an EtherCAT fieldbus that can be configured as Profinet:
- Based Control of Drive-Based Control (CiA402)
Control via motion controllers such as the Trio MC4N motion controller or controllers with CoDeSys V3 as the Stober MC6 controller.
Drive-Based Control with PLCs.
The SI6 controllers can be equiped with STO via hardware terminals or FailSafe over EtherCAT (FSoE). The SI6 meets the highest safety Level e (Cat. 4) according to EN 13849-1.
Bending machine for cold forming of tubes and profiles in draw bending operation, driven by Stöber servo drives.
Powerful machines for the production of reinforced concrete where steel is bended and cutted.
A total of 10 pieces servo-drives are used . The EZ servo motors are controlled by the multi-axis servo drives from the SI6 series:
The system is powered by a PSA634 power supply (50A) whereby energy fed is mutually distributed via the Quick Link DC bus at the rear of the drives.
Overall width in the control of the 10-axis system, including the power supply, is 9 x 65 mm = 585 mm.
The servo drives are controlled via the control based Ci402 protocol from a CoDeSys controller via EtherCAT.
With the Slitting machine glass fiber reinforced plastic can be cut. Hereby the rolls can be determined by both length and width.
Servo drives are used for the throughput of the material, positioning and turning the slit units. This way the production speed and the synchronous operation are fully matched to each other. The Stöber helical-bevel servo gear units were chosen because of their compact installation and hollow mounting shafts.
The software engineers at ATB Automation assist in programming and commissioning via the help desk or on site
Besides control with I/O the drive can also be controlled with EtherCAT and ProfiNet.
The SD6 drive also has the CANopen option available.
This controller can be controlled with a display via Modbus, Profinet or EtherCAT. Click here for more information.
We supply slewing ring bearings, oscillating mountings, tensioner devices from stock and we also have spiral bevel gearboxes, servo gears and electromechanical actuators in our delivery program.
In addition we also select and offer the right components and systems for motion control solutions, such as servo gear motors, linear servo actuators and complete XYZ cartesian systems.
ATB Automation uses cookies to give you the best browsing experience possible on our site.
Continue to use the site as normal if you agree to this.
We use cookies on our website to create the most effective website possible for our users. Cookies are small text files that are sent to and stored on your computer, smartphone or other device for accessing the internet, whenever you visit a website. Cookies allow for us to measure and personalise. The cookies we use allow us to improve your experience when using our website and ensure the website performs as you expect it to. It also allows us to offer eg videos on our website and display social media share buttons. On this site, the cookies we use include 'analytics' cookies, to analyse how users use this site to help us make our website better for those who visit it regularly.
The settings below allow you to specify which cookies you accept. Please note that by not accepting all cookies, some parts of the site will not work properly.