2024
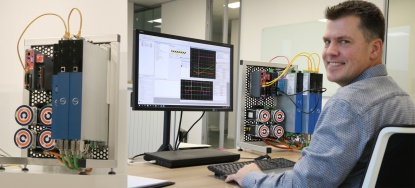
From challenge to opportunity with Stöber safety technology
A safe machine with minimal downtime, without compromises on performance because safety techniques throw a spanner in the works. “That sounds...
Date: 7 April 2023
With its fourth generation of PH series servo planetary gear units, STOBER presents precision gear units that are the largest on the market in their performance class. These feature not only impressive precision but also energy efficiency.
"Of course, we also offer the variant as a geared servo motor," says Artur Wagner, Head of Development for gear units and motors at STÖBER Antriebstechnik, who designed the new generation with his team. "The planetary gear units can be combined, for example, with the compact synchronous servo motors of the EZ series and be mounted directly—without adapters." This is also an enormous competitive advantage: Since the motor adapter is not required, the mass moment of inertia is lower. This allows the full dynamics of the drive to be utilized.
With STOBER motor adapters, all suitable third-party motors can be attached to the gear unit series. For this purpose, the drive specialist offers a special interface technology: The adapters are available with different couplings as well as in the ServoStop variant with an integrated brake. And with the extra-large motor plate of the Large version, the user can connect motors with a very large design. If required, the PH gear units can of course also be combined with a driving angle stage.
One of the companies relying on the large PH gear units combined with third-party motors is ILLIG Maschinenbau GmbH & Co. KG from Heilbronn for its RDM series thermoformer. This series processes foils from the roll or directly in-line from the extruder. The STOBER solution increased the clamping force of the lower table by 50 percent, which significantly increases productivity.
"Planetary gear units are the premier class of gear units," says Wagner. "We have been one the specialists in this field since the 1980s." The components are compact in design and can transmit high torques because, unlike conventional gear units, the power is distributed among several gears. In addition, the designers succeeded in reducing the new PH gear units by up to 100 millimeters. This has a positive effect on the rigidity and mass inertia. "The fourth generation requires less installation space, is lighter and in some cases offers around 20 percent more torque—a real customer advantage," the STOBER expert is convinced.
The excellent housing and gearing quality ensure up to eleven percent higher acceleration torques as well as the highest running accuracy and precision at the same time. Users also benefit from an increased breakdown torque of 50 percent. This is ensured by large tapered roller bearings, which can absorb high external forces and breakdown torques. In addition, there is a very high tilting stiffness.
"In order to increase parameters such as acceleration torque, power density and torsional stiffness, we have widened or more generously dimensioned the planetary gears for certain gear ratios," Artur Wagner describes. State-of-the-art materials and hardening processes are used for the planetary gears and sun pinions. This makes the PH series highly stable and robust. For the user, this means extremely little effort for service and repair—and this with reliable and consistently high performance. This is also ensured by high-quality lifetime lubrication with synthetic gear oil.
Wagner continues, "Our new planetary gear units have a gear ratio range of 12 to 600. This makes them particularly versatile in use." In addition to the default version of the new PH gear units, STOBER also offers a Quattro design: The PHQ series with an innovative four-planet system is extremely precise due to its high-quality helical gearing and offers even greater torsional stiffness. The user also benefits from maximum torque. On request, STOBER also combines the fourth generation with rack and pinion drives of the ZTR and ZTRS series. Thus, the specialist supplies high-performance geared motors—ideally suited for use in feed axes of machine tools.
"Energy efficiency is becoming increasingly important, especially in light of rising electricity costs. In combination with the EZ synchronous servo motors, our customers benefit from high efficiency," Artur Wagner emphasizes. Especially manufacturers of premium injection molding machines and precision presses rely on this. "Our new planetary gear units are therefore in demand wherever size, precision, cost effectiveness and efficiency play a role," the STOBER chief designer describes. "In addition, they are exceptionally resilient to high alternating loads—for example, for opening and closing injection molds weighing several tons in plastics processing."
"A high-quality appearance is becoming increasingly important on the market," Artur Wagner notes. The drive specialists have therefore optimized the design of the new generation and adapted it to the family of STOBER planetary gear units, including the smaller PH sizes. The contours flow better and the surface structure is considerably smoother. "Now, the appearance matches the inner values of the gear units as well," Wagner says with a chuckle. And these values pack a punch.
The new generation is equipped with an electronic nameplate: In combination with the STOBER electronics, each geared motor automatically sends its electronically and mechanically relevant data to the associated drive controller via plug-and-play during commissioning. As a result, the geared motors are uniquely identified. This eliminates high-effort, error-prone parameterization, which shortens the total system configuration significantly.
STOBER benefits from more than 85 years of experience in the design and production of drive components. Paul and Wilhelm Stöber founded the company as a mechanical workshop in 1934. They were both driven by the desire to implement their own ideas and optimize things they thought could be improved—at least, that is how it has gone down in company history. This spirit still defines the company today. The entire product portfolio—from mechanics to electronics—stands for quality, durability, sustainability.
Thus, the specialist is also able to implement the complete drive train in-house. If needed, customers receive the complete drive solution consisting of gear unit, motor, electronics and the cables—in any possible combination. The necessary areas of the company work together for this like precise gears. As a result, managers from the individual departments are constantly in contact with each other, as are the commissioning engineers and customer support representatives. These short paths create efficiency, effectiveness and precision. "With SI6 and SC6, for example, we always have the right drive controller at hand—as well as the optimum power and encoder cable or our innovative One Cable Solution," Artur Wagner promises.
Arthur Wagner is head of "Gear Unit and Motor Development" at STÖBER Antriebstechnik in Pforzheim.
We supply slewing ring bearings, oscillating mountings, tensioner devices from stock and we also have spiral bevel gearboxes, servo gears and electromechanical actuators in our delivery program.
In addition we also select and offer the right components and systems for motion control solutions, such as servo gear motors, linear servo actuators and complete XYZ cartesian systems.
ATB Automation uses cookies to give you the best browsing experience possible on our site.
Continue to use the site as normal if you agree to this.
We use cookies on our website to create the most effective website possible for our users. Cookies are small text files that are sent to and stored on your computer, smartphone or other device for accessing the internet, whenever you visit a website. Cookies allow for us to measure and personalise. The cookies we use allow us to improve your experience when using our website and ensure the website performs as you expect it to. It also allows us to offer eg videos on our website and display social media share buttons. On this site, the cookies we use include 'analytics' cookies, to analyse how users use this site to help us make our website better for those who visit it regularly.
The settings below allow you to specify which cookies you accept. Please note that by not accepting all cookies, some parts of the site will not work properly.