2024
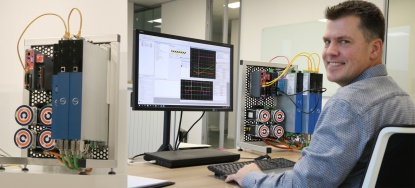
From challenge to opportunity with Stöber safety technology
A safe machine with minimal downtime, without compromises on performance because safety techniques throw a spanner in the works. “That sounds...
Date: 8 May 2024
Did you know that gear racks were originally used to place objects at different heights? For example, they were used in kitchens to perfectly position pots over fireplaces. As industrialization progressed, the gear rack became more important as a machine element and found its way into mechanical engineering.
Today, rack and pinion drives convert the rotary movements of gear units or motors into linear movements, or vice versa. The drive itself consists of a gear rack and its counterpart, the pinion. When the pinion is turned, the gear rack moves along its longitudinal axis, resulting in linear motion.
Gear racks must not shift out of place when forces are applied by the pinions. The pressing force of the screw fastenings counteracts this. In addition, gear racks are usually mounted with dowel pins at both ends of the racks. This process requires considerable effort. To ensure that the position is exactly right, the bores for the dowel pins must be made and then reworked with a reamer directly on the machine in the bolted-on state. This is extremely demanding, time-consuming work, especially on very complex systems.
Our new precision gear racks with twice the bores eliminate the need for time-consuming pinning. The contact pressure on the machine body is doubled: Instead of every 125 millimeters as usual, gear racks are fastened again after just 62.5 millimeters. Although time-consuming pinning is not required, it remains an option thanks to the existing pin bores. This provides increased safety. And maximum ease of installation.
Our precision gear racks are available in various lengths and modules, for the highest demands on smooth operation and positioning accuracy.
„These smart, high-quality solutions have rounded off the lower end of our mechanical system. And for each user, everything fits together perfectly.”
Director of Business Development Asia Pacific at STOBER
We supply slewing ring bearings, oscillating mountings, tensioner devices from stock and we also have spiral bevel gearboxes, servo gears and electromechanical actuators in our delivery program.
In addition we also select and offer the right components and systems for motion control solutions, such as servo gear motors, linear servo actuators and complete XYZ cartesian systems.
ATB Automation uses cookies to give you the best browsing experience possible on our site.
Continue to use the site as normal if you agree to this.
We use cookies on our website to create the most effective website possible for our users. Cookies are small text files that are sent to and stored on your computer, smartphone or other device for accessing the internet, whenever you visit a website. Cookies allow for us to measure and personalise. The cookies we use allow us to improve your experience when using our website and ensure the website performs as you expect it to. It also allows us to offer eg videos on our website and display social media share buttons. On this site, the cookies we use include 'analytics' cookies, to analyse how users use this site to help us make our website better for those who visit it regularly.
The settings below allow you to specify which cookies you accept. Please note that by not accepting all cookies, some parts of the site will not work properly.