2024
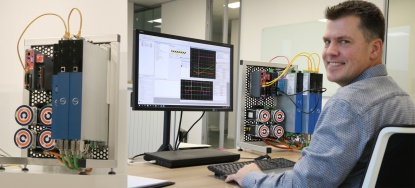
From challenge to opportunity with Stöber safety technology
A safe machine with minimal downtime, without compromises on performance because safety techniques throw a spanner in the works. “That sounds...
Flexible and affordable expansion of a large number of safety functions for the Stöber SD6 servo drive in accordance with EN 61800-5-2. With the PASmotion software from Pilz integrated in the DriveControl Suite setup software from Stöber, the specialist knowledge and experience of two worlds come together.
With as result a simple and flexible setup of safety functions for STOP, MOTION, MONITORING, BRAKE, RESTART and STATUS in Stöber's high performance stand alone SD6 servo drive.
The SD6 servo drive with the SE6 safety module included, can be integrated in the safety circuit as a safety related part of the control system (SRP / CS) for the implementation of safety functions (Safe Drive System).
The table below shows an overview of the safety functions according to EN 61800-5-2 and which are available with the SE6 safety module.
A Safe Drive System consists of:
Optionally can be added:
Example activation safety function (SS1) with fault detection by status feedback
Pilz PASmotion software tool started from Stöber DriveControl Suite
Example configuration Safe Operating Stop (SOS) function in PASmotion
The software engineers at ATB Automation assist in programming and commissioning via the help desk or on site
We supply slewing ring bearings, oscillating mountings, tensioner devices from stock and we also have spiral bevel gearboxes, servo gears and electromechanical actuators in our delivery program.
In addition we also select and offer the right components and systems for motion control solutions, such as servo gear motors, linear servo actuators and complete XYZ cartesian systems.
ATB Automation uses cookies to give you the best browsing experience possible on our site.
Continue to use the site as normal if you agree to this.
We use cookies on our website to create the most effective website possible for our users. Cookies are small text files that are sent to and stored on your computer, smartphone or other device for accessing the internet, whenever you visit a website. Cookies allow for us to measure and personalise. The cookies we use allow us to improve your experience when using our website and ensure the website performs as you expect it to. It also allows us to offer eg videos on our website and display social media share buttons. On this site, the cookies we use include 'analytics' cookies, to analyse how users use this site to help us make our website better for those who visit it regularly.
The settings below allow you to specify which cookies you accept. Please note that by not accepting all cookies, some parts of the site will not work properly.