2024
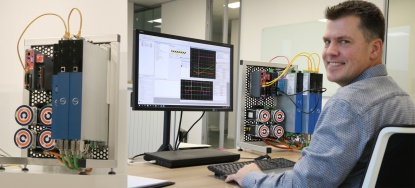
From challenge to opportunity with Stöber safety technology
A safe machine with minimal downtime, without compromises on performance because safety techniques throw a spanner in the works. “That sounds...
Date: 1 April 2013
The poor efficiency of compressed-air makes use of pneumatic actuators costly. The University of Kassel examined the difference in efficiency between electromechanical and pneumatic actuators and concludes that the electromechanical technology is far more cheaper to use. In this study they used the IAI RoboCylinders electromechanical actuators.
Efficient energy consumption
Rising energy costs, growing climate awareness of companies and higher technical demands of production processes, have led to much more emphasis on energy conservation the last few years. It is known that a pneumatic actuator in the purchase is much cheaper than an electromechanical actuator. The energy consumption of these two different technologies is often less well known. Only when that is known, one can decide on the actual costs and the impact on our environment.
Comparison pneumatic versus electric linear actuator
At the department of Environmental Responsible Products and Processes of the University of Kassel, they deployed studies on this matter. They have positioned an electric linear actuator next to a pneumatic cylinder, carrying out the same motion functions. The cylinders are chosen such that they exhibit similar specifications. They are both provided with a slide, have an effective stroke length of 50 cm and can move a maximum load of 12 kg. The research has opted for a load of 2.0 kg. The electric cylinder is powered by a 24V stepper motor driving a ball screw spindle. The pneumatic cylinder is a rodless cylinder.
Initial investment
Looking at the costs: The electromechanical cylinder with an investment of around sixteen hundred Euro is about five hundred euros more expensive than the pneumatic system. This takes into account all necessary components such as controls, cables and hoses. The pneumatic solution will therefore win in this area.
Energy-related comparison
For energy related comparison of the cylinders, they are both equipped with sensors. The energy of the electric cylinder (including control) will be immediately and easily recorded with a power sensor. The required amount of air for the pneumatic cylinder is measured with a flow meter. This is based on a moderately efficient compressor, which, for the compression of one cubic meter, needs about 130 Wh.
Factor 15 diffence compared to pneumatic cylinders
Assuming six thousand operating hours per year (similar to a three shift work), the energy demand of the pneumatic cylinder amounts to 4212 kWh per year. The electric cylinder consumes only 270 kWh per year. The electric cylinder thus performs a factor fifteen better than the pneumatic cylinder.
That usage translates into CO2 emissions of respectively 2.5 tonnes and 155 kg per year (assuming 575 g CO2/kWh). At an electricity price of ten cents per kWh, this is an energy price tag of respectively 421 and 27 Euro. The higher investment costs of the electromechanical cylinder are thus earned back within sixteen months.
Comparison pick and place system
In order to measure the effect of a situation which is even more similar to a production process, a second experiment was carried out. Handling of a product was examined, where not only linear displacements are applied. Pick and place systems require besides translations and rotations also gripper motion. Here, also a test setup was created with pneumatic systems and with electromechanical systems of IAI. The results of that comparison again speaks for itself (see graph). Again in this application, we see savings of approximately 95 percent. The difference in operating expenses (936 against 40 Euro) allows a user to earn back the higher investment (9,500 to 14,500 euros) in 5.5 year.
Savings potential operating costs
These studies show a clear savings potential in operating costs if users decide to replace their pneumatic components. And we're not even taking into account yet the fact that maintenance and repair costs for the electromechanical actuators are also significantly lower.
+31 297 38 05 54
martin@atbautomation.eu
We supply slewing ring bearings, oscillating mountings, tensioner devices from stock and we also have spiral bevel gearboxes, servo gears and electromechanical actuators in our delivery program.
In addition we also select and offer the right components and systems for motion control solutions, such as servo gear motors, linear servo actuators and complete XYZ cartesian systems.
ATB Automation uses cookies to give you the best browsing experience possible on our site.
Continue to use the site as normal if you agree to this.
We use cookies on our website to create the most effective website possible for our users. Cookies are small text files that are sent to and stored on your computer, smartphone or other device for accessing the internet, whenever you visit a website. Cookies allow for us to measure and personalise. The cookies we use allow us to improve your experience when using our website and ensure the website performs as you expect it to. It also allows us to offer eg videos on our website and display social media share buttons. On this site, the cookies we use include 'analytics' cookies, to analyse how users use this site to help us make our website better for those who visit it regularly.
The settings below allow you to specify which cookies you accept. Please note that by not accepting all cookies, some parts of the site will not work properly.