2024
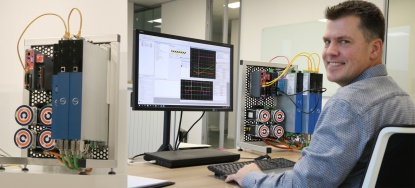
From challenge to opportunity with Stöber safety technology
A safe machine with minimal downtime, without compromises on performance because safety techniques throw a spanner in the works. “That sounds...
Date: 17 September 2020
In many cases an electric actuator is an excellent alternative for a hydraulic cilinder. Even though the linear electric actuator establishes more and more, I do regularly receive certain questions from customers considering eletric actuators. In this blog I will eleborate on the 5 most frequently asked questions.
Hydraulic actuators have some advantages in certain cases. They have a high power density, low component acquisition cost, moderate to high stiffness, high speed, and are a commonly used technology with several commercial outlets. However, in certain situations, hydraulic actuators can be less beneficial to a system. They have a moderate accuracy and repeatability without the additional help of extra tuning equipment.
They also have intricate and complex installation and maintenance due to hydraulic pumps and tubing. Additionally, they have a high installation cost, low energy efficiency, large environmental impacts, and limited scalability and modularity. These are the cases where electric actuators offer a better solution..
Electric actuators offer high speed and force, are flexible and easily programmable for a variety of load conditions, have high accuracy and repeatability, are efficient, simple to install, require little maintenance, and are environmentally friendly.
By not using a hydraulic system, the user can eliminate oil leaks, reduce pollution, and improve worker safety.
Other environmental benefits of electric actuation include:
There are certain conversion challenges that occur when converting from hydraulic actuator systems to electric ones. If the system has more than one hydraulic actuator, the approach of a piecemeal conversion may be a more difficult process as compared to converting all machine axes at the same time.
If you have harsh loading conditions, you should consider bumpers or adjusting the motion profile to alleviate impact shock loads and high vibration.
Converting properly from one actuating method to another requires understanding how to properly size the new actuator. The actual stroke length should be measured and considerations toward mounting should be taken. For a simple estimate of required force, the piston diameter multiplied by the pump pressure should guide your electric actuator selection process between choosing the ideal measured force and the acceptable calculated force. The engineer should know the speed (measured time required for extend over retract), how many cycles per minute, hour, and day, number of shifts or days per week the actuator is used, and the operational environment. The operational environment will include the temperature, dust, liquid, and hazard conditions.
Advances in electromechanical actuation include the pairing of a rotary servo motor coupled with rotary-to-linear mechanical transmission such asa roller screw. Roller screws have nuts running along a threaded rod that are geared with respect to each other and a nut housing much like a planetary gearbox.
This leads to some significant advantages of the electric roller screw actuator:
Along with the pairing of servo motors and roller screws, advances in brushless motors with feedback devices provide higher accuracy and repeatability.
Traditional electric actuators typically use single or three-phase induction motors as their driving force. The problem with this design is when the actuator needs to change directions or start and stop, the operation is limited by motor temperature rise and therefore has limited duty cycles. Using a continuous-duty-cycle brushless dc motor along with the paring of roller screws helps solve this limitation. The feedback device allows for very precise control of both the position and speed of the actuator output rod.
Many industries are using electric lineair actuators to their benefit in systems. For example they are used in the automotive, graphics, food and process industries, such as welding equipment, dosing and filling applications, press applications, etc.
Machines in the foodprocessing industries use electric actuators for filling machines, producing blocks, transporting and indexation of products.
The oil- and gasindustry use electric actuators to replace hydraulic and pneumatic actuators thanks to their environmental benefits and flexible and accurate control. Both hydraulics and pneumatics are at risk of leakage, resulting in dangerous situations (e.g. contamination or flammable gas where methane usually is used as the pneumatic fluid in the oil field). Electric actuators are increasingly used to solve all these problems.
A wide range of benefits in may situations that benefit from the use of electric actuators. Became curious? Or talk about an application? Please contact me!
+31 297 38 05 54
martin@atbautomation.eu
We supply slewing ring bearings, oscillating mountings, tensioner devices from stock and we also have spiral bevel gearboxes, servo gears and electromechanical actuators in our delivery program.
In addition we also select and offer the right components and systems for motion control solutions, such as servo gear motors, linear servo actuators and complete XYZ cartesian systems.
ATB Automation uses cookies to give you the best browsing experience possible on our site.
Continue to use the site as normal if you agree to this.
We use cookies on our website to create the most effective website possible for our users. Cookies are small text files that are sent to and stored on your computer, smartphone or other device for accessing the internet, whenever you visit a website. Cookies allow for us to measure and personalise. The cookies we use allow us to improve your experience when using our website and ensure the website performs as you expect it to. It also allows us to offer eg videos on our website and display social media share buttons. On this site, the cookies we use include 'analytics' cookies, to analyse how users use this site to help us make our website better for those who visit it regularly.
The settings below allow you to specify which cookies you accept. Please note that by not accepting all cookies, some parts of the site will not work properly.