2024
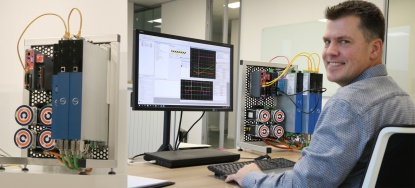
From challenge to opportunity with Stöber safety technology
A safe machine with minimal downtime, without compromises on performance because safety techniques throw a spanner in the works. “That sounds...
Date: 2 April 2019
The company AME in Eindhoven makes various products for various customers. The volumes of the products are such that with a sufficient degree of automation production in the Netherlands is possible. In addition, AME is constantly looking for opportunities to improve its production processes.
Yves Elmensdorp (system engineer at AME) has as a graduation assignment at which he looked at the possibilities for improving the production process at AME by applying a generic 3-axis robot. Part of this assignment was to make a robot. This could be for testing or for assembly. We looked at actuators, a certain precision and certain specifications in order to achieve a good result. Hereby Yves came into contact with ATB Automation where they have both the hardware and the knowledge of motion control which are needed with such a system.
The 3-axis robot
We can take a look at the AME workroom where we can find the metalworking machines and robots for assembly and where the 3-axis robot (the graduation assignment) is set up. Before entering the workroom we are given a blue cotton jacket and grounded straps must be put on and in our shoes to prevent static electricity and ESD shocks (Electro Static Discharge). The workroom is spacious and clean and we walk to the 3-axis robot.
The application is a 3-axis robot system in the form of an H-bridge. This means that there are 2 X axes, a Y axis and a Z axis. Specific to this project was the desire to make a generic system, which can be used for various products and production processes. "In our case this means that you have a specific product plate. A kind of holder of the product where a specific tool can be put on the robot without having to rebuild the entire robot. The only thing you should do is to remove a plate from the bottom plate and put a new one on it without having to screw it on and put a specific tool on the robot. We have made up a kind of generic holder for that where you can easily put on a new tool with 4 screws. We are actually so far now that with a new version it comes down to a piece of logic", says Yves Elmensdorp.
There is a piece of logic in the robot with which a check is done, a kind of ID recognition. This allows you to see in the software whether the right tool and the correct product plate are on the robot, so that you can catch errors. This requires an intelligent control that can also control the 3-axis robot flexibly and accurately.
A good combination
AME has found a supplier in ATB that provides good advice in the preliminary process and also provides them with the necessary advice and support in the follow-up process. "When we started with the first version, the input and expertise of ATB Automation about the project helped us a lot. This has turned out to be a positive experience," says Yves. Based on the specifications, ATB calculated which IAI RoboCylinder linear axes were suitable for the 3-axis robot. For the X-axes and the Y-axis we have come to the RCP6-SA types with slides and for the Z-axis the RCP6-TA has been chosen which is equipped with a robustly guided table and is therefore very suitable for vertical applications. In addition, ATB advised on the possibilities for applying a motion controller whereby it was possible to run other applications directly on that platform. The result was the application of the TRIO PC-MCA, an industrial PC with integrated motion controller. The TRIO Flexslice modules were used for controlling the linear axes and extending digital and analog I / O.
The IAI RoboCylinder linear axes and the TRIO PC-MCAT fit well with the precise nature of the application. The desired accuracy is more than achieved in practice by the combination of the precision of the IAI linear axes and the possibilities that the TRIO motion controller offers for programming precise interpolated movements.
‘ATB Automation is a good supplier. A great company in terms of support and communication. The technical support of the application engineers is fast and above all good. Also the sales support is flexible and reliable due to the high technical level.’
The use of vision
A combination with Vision was used for the first development of the 3-axis robot. Yves says: "We use a camera to align a certain product, for example. For gluing an object, for example a glass plate, you want to be at a certain precision for example 10 µm. If your product is skewed by a few micrometers, which can happen due to inaccuracies in the holder, your glue pad will also go wrong. For an application with adhesives, we opt for a setup with a camera, because then you can see certain recognition points and with that you can straighten the software and get to your precision." We could easily connect this vision system directly to the Trio PC-MCAT.
Future plan
AME makes its own user interface on the generic 3-axis robot in a C-sharp environment that runs on the PC-MCAT. This software communicates with the motion controller part. "The future plan is to place 3-axis robots against a 6-axis robot. The 6-axis robot is then only for "handling". The 6-axis robot, for example, grabs a piece of glass or a piece of plastic and places it with a 3-axis robot. The 3-axis robot is then controlled from a central system. The central system sends standardized commands to the motion controller for translation. That is our plan now. We have already carried out tests in which we send standardized commands from another computer to the 3-axis and the robot picks it up perfectly," says Yves.
Who is AME?
AME stand for Applied Micro Electronics and is an independant developer and producer of electronic products of high quality in the top of the technological world (Brainport Eindhoven). Many different products are made and the work surface is wide, from automotive till energy with for example energy converters. ‘We actually make the products for everything that contains products. For one customer this can be a PCB and for another customer this can be a design, but it can also be the entire assembly. Suppose a customer want to have a user interface and he has an idea. We get started and produce it here, says Yves Elmensdorp.
The goal of AME is to make innovative products that exceed customer expectations. The support from ATB Automation has helped really good.
We supply slewing ring bearings, oscillating mountings, tensioner devices from stock and we also have spiral bevel gearboxes, servo gears and electromechanical actuators in our delivery program.
In addition we also select and offer the right components and systems for motion control solutions, such as servo gear motors, linear servo actuators and complete XYZ cartesian systems.
ATB Automation uses cookies to give you the best browsing experience possible on our site.
Continue to use the site as normal if you agree to this.
We use cookies on our website to create the most effective website possible for our users. Cookies are small text files that are sent to and stored on your computer, smartphone or other device for accessing the internet, whenever you visit a website. Cookies allow for us to measure and personalise. The cookies we use allow us to improve your experience when using our website and ensure the website performs as you expect it to. It also allows us to offer eg videos on our website and display social media share buttons. On this site, the cookies we use include 'analytics' cookies, to analyse how users use this site to help us make our website better for those who visit it regularly.
The settings below allow you to specify which cookies you accept. Please note that by not accepting all cookies, some parts of the site will not work properly.