2024
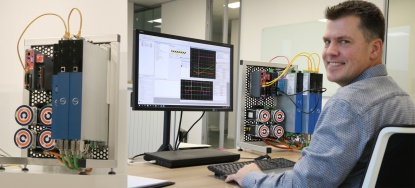
From challenge to opportunity with Stöber safety technology
A safe machine with minimal downtime, without compromises on performance because safety techniques throw a spanner in the works. “That sounds...
The Flex-6X Nano is the improved version of the Flex-6 Nano. With the new 64 bit Dual Core 1.2 GHz ARM Cortex A55 Processor, this flexible and compact stand-alone motion controller is even more powerful. The internal 1 GB DDR3 memory can be expanded to 32 GByte using a Micro SD card.
The Flex-6X Nano can be used as a stand-alone EtherCAT controller or can be connected directly to the Trio EtherCAT Flexslice system. In addition to synchronous control of EtherCAT servo drives, the system can be expanded to control stepper drives with pulse and direction, binary and analog I/O and other functionality that meets the EtherCAT standard.
The Flex-6X Nano is available for controlling 2, 4, 8, 16, 32 or 64 motor axles. All versions have 64 software axes that can be used as virtual axis or via EtherCAT as hardware-assigned servo or stepper axes or encoder input axes. Each axis can be programmed with linear, circular or helical or spherical interpolation, electronic cams and coupled axes.
The built-in Ethernet port can be used for programming and connection of the common HMI (Trio touch screen). But also for communication with a main controller via Profinet, Ethernet-IP, Modbus TCP-IP etc.
Programming and commissioning of the Flex-X Nano is done using the powerful Motion Perfect development environment. With the help of multi-tasking application software, complex movements are easily programmed with the Trio MOTION-iX commands and integrated HMI editor. In addition, the standard IEC 61131-3 programming language is available for the development of a fully functional PLC program. The result is tested and optimized with the help of a motion controller simulator, HMI simulator, the 3D oscilloscope and 3D machine visualization tool.
The Flexslice input / output modules from Trio offer a robust, fast and flexible solution for both motion control and general automation. EtherCAT cycle times up to 125μsec are supported and the bus coupler uses EBUS technology to bring all submodules to the EtherCAT network without degrading performance.
EtherCAT slave nodes (Flexslice modules) are connected via the Flexslice EBUS and the EtherCAT connector. Total number of slave nodes can be up to 128 including I / O and more complex devices.
Flexslice modules:
ATB Automation supplies motion controllers from Trio Motion Technology and Leadshine. The Trio motion controllers can also be easily extended with various I / O and control panels so that the controller also can operate as stand-alone machine controller .
More information about motion controllers.
We supply slewing ring bearings, oscillating mountings, tensioner devices from stock and we also have spiral bevel gearboxes, servo gears and electromechanical actuators in our delivery program.
In addition we also select and offer the right components and systems for motion control solutions, such as servo gear motors, linear servo actuators and complete XYZ cartesian systems.
ATB Automation uses cookies to give you the best browsing experience possible on our site.
Continue to use the site as normal if you agree to this.
We use cookies on our website to create the most effective website possible for our users. Cookies are small text files that are sent to and stored on your computer, smartphone or other device for accessing the internet, whenever you visit a website. Cookies allow for us to measure and personalise. The cookies we use allow us to improve your experience when using our website and ensure the website performs as you expect it to. It also allows us to offer eg videos on our website and display social media share buttons. On this site, the cookies we use include 'analytics' cookies, to analyse how users use this site to help us make our website better for those who visit it regularly.
The settings below allow you to specify which cookies you accept. Please note that by not accepting all cookies, some parts of the site will not work properly.