Jul
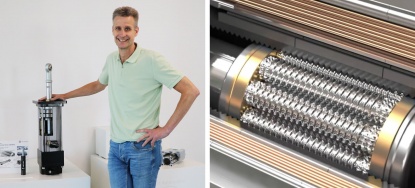
Roller Screw versus Ball Screw Actuators
In the ever-evolving field of engineering, roller screw technology has become a significant force in linear electric actuator motion control....
Date: 8 September 2015
Recently I was grocery shopping on Saturday morning, when I got a phone call at 9 am by Groener Elektrotechniek. His client Betonson in Kampen produces 24/7 and Stöber servo motors and servo drives in use in several machines. Precisely on Saturday morning an error message appeared on one of the drives, which is coupled to the servo motor. Now what? The brake of a 12 years old servo motor failed, resulting in a production downtime. After the call from his customer, Greener called us, hoping he could reach us. Fortunately, we have 24-hour standby service and Mr. Groener could actually get in contact with us.
In consultation with the customer, we discussed the options. One option was to only replace the brake, but then the encoder would have to be dismantled and a new one should be delivered from Germany. And to replace an absolute encoder, you need sophisticated equipment for the fine-tuning of the encoder. All this would take too much time. The best solution in my opinion would be to deliver a new servo motor as soon as possible from Stober Germany (Pforzheim). On my return home around 9:30 am I logged on immediately - hurrah for telecommuting - and I called the service line from Stober.
The Stober call center noted all the relevant data and within a quarter hour the Stober head of service called me back. Subsequently he immediately made all arrangements necessary with the assembly technicians who had weekend shift at that time. Therefore assembly of the servo motor could already be started at 10 am. Meanwhile, the courier was already organized, so that the serv motor could be delivered to the home of the Betonson technician.
At 10:30 hours I could already contact our customer with great news: "Everything is taken care of!". Moments later, the assembly of the servo motor was ready, so just 3 hours after the notification of the failure the courier drove away from Pforzheim with the newly assembled servo motor. Thanks to the 24-hour availability of Stöber and us, the mechanic of Betonson got the servomotor delivered home around 18:00, ready for installation. Several hours later, the factory was back in full production.
+31 297 38 05 64
quality@atbautomation.eu
Johan Trompert is service engineer motion control and quality manager. Since 1988 Johan has been responsible for the engineering and construction of control cabinets, service and support to frequency inverters, servo drives and motion controllers at ATB Automation. In addition, he is responsible for monitoring and maintaining the ISO 9001 quality management system.
We supply slewing ring bearings, oscillating mountings, tensioner devices from stock and we also have spiral bevel gearboxes, servo gears and electromechanical actuators in our delivery program.
In addition we also select and offer the right components and systems for motion control solutions, such as servo gear motors, linear servo actuators and complete XYZ cartesian systems.
ATB Automation uses cookies to give you the best browsing experience possible on our site.
Continue to use the site as normal if you agree to this.
We use cookies on our website to create the most effective website possible for our users. Cookies are small text files that are sent to and stored on your computer, smartphone or other device for accessing the internet, whenever you visit a website. Cookies allow for us to measure and personalise. The cookies we use allow us to improve your experience when using our website and ensure the website performs as you expect it to. It also allows us to offer eg videos on our website and display social media share buttons. On this site, the cookies we use include 'analytics' cookies, to analyse how users use this site to help us make our website better for those who visit it regularly.
The settings below allow you to specify which cookies you accept. Please note that by not accepting all cookies, some parts of the site will not work properly.